High efficiency, excellent controllability, and freedom of arranging hydrostatic drive components independently from each other allow for a significant reduction of costs when generating renewable energies. The established cost analysis from the US Department of Energy (NREL- LWST COE) for the new Hydrostatic Wind Turbine reduces the costs of energy ($/kWh) of current Wind Turbines (2011) with 132% by 21.7% to 109.3% - closing the gap by 70% when compared with a conventional power plants (100%). Noticeable additional cost benefits can be achieved when applying the Hydrostatic Wind Turbine in new offshore installations.
Nacelle
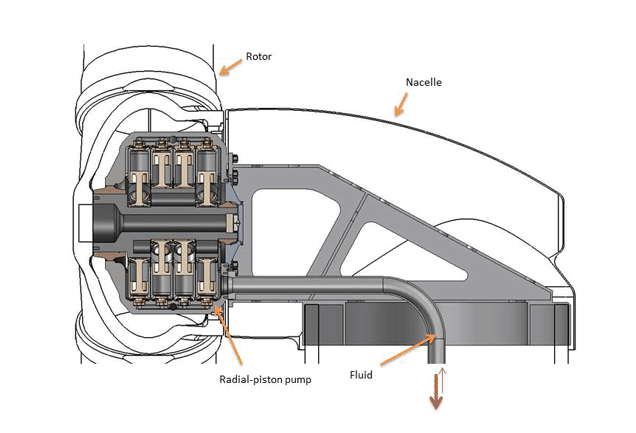
Ground Station
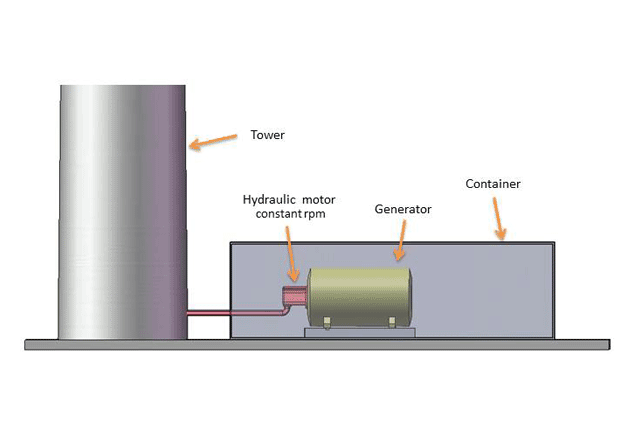
|
MW |
RPM |
Weight |
Dimensions |
Turbine |
5.0 |
18 |
4,300 lbs. (1.950 kg) |
Ø 98“x 78“ (ø 250 x 198 cm) |
Hydraulic Motors |
3.7 |
1,800 |
1,120 lbs.(510 kg) |
Ø 25“x 29“ (ø 64 x 74 cm) |
|
1.7 |
1,800 |
595 lbs. (270 kg) |
Ø 20“x 23“ (ø 51 x 58 cm) |
An efficient utilization of wind power is a simple transmission of large powers at low, variable speed (rotor) into high speed with constant revolutions of the infinitely adjustable hydraulic drive motor (generator). Locally separated power input and output simplifies the arrangement of the drivetrain and reduces the cost for manufacturing, installation, and maintenance of the wind turbine. The new hydrostatic drive is not reactive to deformation and vibrations since all bearings are self-adjusting hydrostatic bearings of extremely low friction. Gear boxes and roller bearings are not required and the useful life is not limited.
The new radial-piston pump is located in the hub of the rotor and transmits pressurized hydraulic fluid to the hydraulic motors, driving the electric generator with constant rpm. The motor/generator unit and all additional installations are located in a container on ground level. This reduces the requirements regarding installation, maintenance, space, weight, and resistance to weather conditions, allowing non-turbine-specific components to be utilized. The concept reduces the weight (rotor & nacelle) on top of the tower of a 5 MW turbine by 50% or more, from about 250 to. to 120 to., reducing the cost of the tower and the installation.
To minimize the losses of energy and the stress (deformation) of the turbine, the weight of the rotor is supported by self-aligning hydrostatic bearings. The forces of the radial-piston on the rotor/pump driveshaft are 100% balanced and create no additional bearing loads. The low internal losses and higher allowable speeds increase the yield of energy from the wind. The calculation of losses for the pump result in an efficiency of 96.5%, and for the whole drive train, from rotor to generator shaft, in ca. 89%.
The costs for wind energy become lower with the increasing size of the turbine. However, current assumptions indicate that, for a conventional 12 MW turbine, the weight on top of the tower will exceed 700 to and render large sizes unprofitable. The hydrostatic drive for a 12 MW turbine (15 rpm) weighs about 50 to and reduces the weight on top of the tower significantly, allowing the use of still transportable tower constructions.
The pictures show the cross-section of the radial-piston pump of the rotor hub. The Ground Station is only shown as a concept.
U.S. Patent pending.
Copyright Valentin Technologies