Higher speeds and payloads at reduced cost are needed to noticeably improve air travel for short- and medium distances. This requiers lower weight, air drag and fuel consumption, economically obtainable only with winged aircraft. Current helicopters are not well suited to fulfill these requirements.
Flight Position
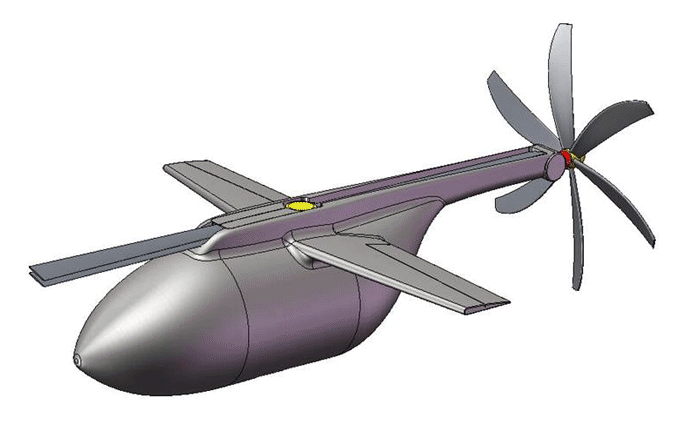
VTOL Position
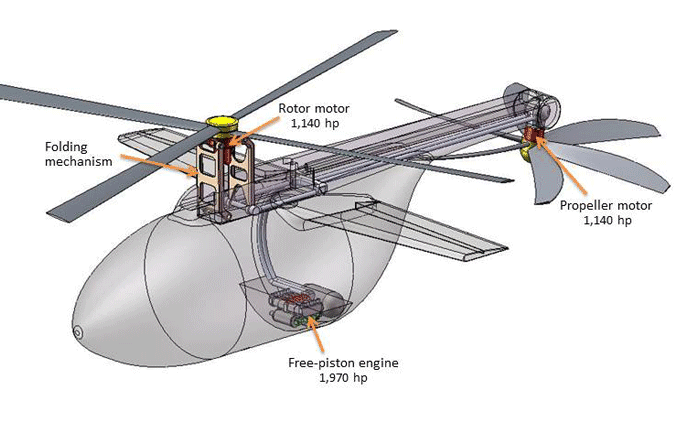
Weight class |
4.0 to |
4.0 to |
Occupants |
1 + 9 |
1 + 9 |
Speed |
270 kt. |
310 mph 500 km/h |
Travel |
1,300 nm |
1,500 miles 2.400 km |
Rotors |
Ø 28’ 6” / Ø13’ |
8,7 m x 4,0 m |
Powertrain |
FPE Engine |
Motors (incl. gears) |
Power |
1.450 kW (1,972 hp) |
2 x 840 kW (1,140 hp) |
Weight |
148 kg (325 lbs.) |
2 x 82 kg (180 lbs.) |
Dimensions |
72 x 64 x 43 cm (28" x 25" x 17") |
ø26 x 39 cm (10" x 15") |
Conventional helicopters reach maximal speeds of about 175 kt. (200 mph, 320 km/h), limited by the reduced speed at the tip of the retreating rotor blade, resulting in air velocities not capable of providing the required lift forces. Counter-rotating coaxial rotors prevent the effect of declining lift for-ces, but are mechanically complex and heavy, increasing air drag, costs, and fuel consumption significantly. Aircraft with tiltable propeller drive/wing systems require rotor/propeller units with a very wide operating range (speed, thrust), resulting in large, complex rotor/propeller drives which are not optimal for horizontal or vertical flight. They are also not practical for conventional start and landing.
Advanced hydrostatic drives have the flexibility and very high power density required for the concept of the new High-Speed Helicopter. The rotor and propeller deliver the thrust for vertical take-off and landing (VTOL) and the transition. In the vertical phase the propeller points toward the landing pad and is slightly tilted sideways to counter the moment of the rotor. During the critical phase of transition, rotor and wing provide sufficiant lifting forces. During horizontal flight at higher speeds, the short wings provide the lift forces and the tiltable propeller in the rear the thrust.
The concept allows for a smaller, simpler rotor, designed only for vertical take-off and low horizontal speeds. At higher speeds, the lifting forces of the wings increase, and the rotor will be shut down, the blades brought into parallel position, and the complete rotor mechanism submerged into the fuselage, reducing the air drag by up to 50%. The sideways tilting of the propeller is discontinued but can be used to change the direction of flight. If needed, a simple tail plane can be added.
The aerodynamic drag of the helicopter, considering the smaller size of the new hydrostatic drive and smaller wings, achieves nearly that of winged aircraft and its high speeds and travel distances. The wing, designed only for higher speeds (not for start and landing) is significantly smaller, and the noise level and comfort (vibrations) are noticeably improved.
The 3-Cylinder Hydraulic Free-Piston Engine (HFPE) achieves significant improvements in specific power (kW/kg / hp/lbs.) and a reduction in fluid flow pulsation, as required for operations without an accumulator. The weight is about 35% lower than that of a turboshaft engine and the lower con-sumption reduces the weight of fuel by about 35%. The weight of the HFPE is based on Titanium housings. The drivetrain components are shown in scale.
U.S. Patent pending.
Copyright Valentin Technologies